Ökologisch optimierte Bento-Boxen
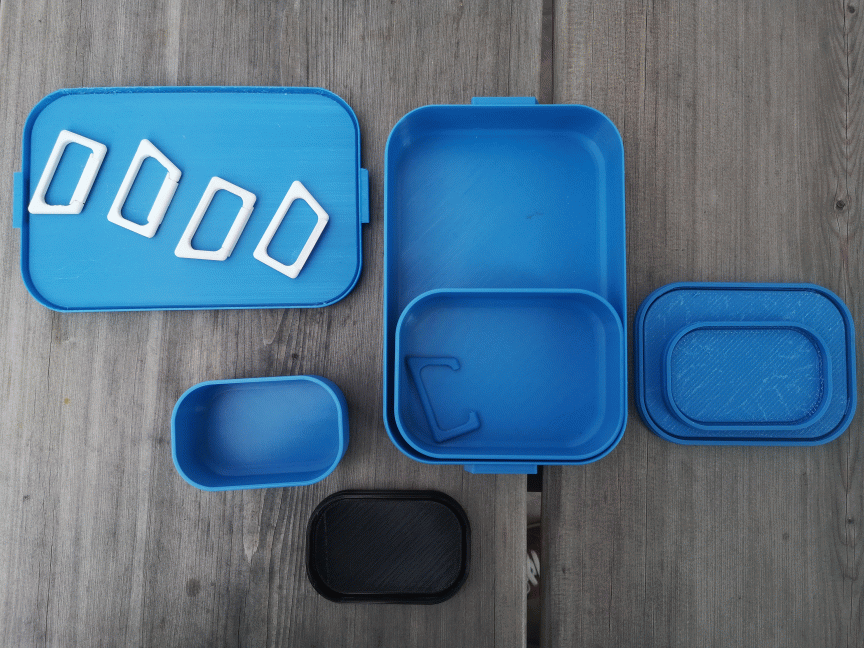
Mit der CO₂-Bilanz existiert ein Maß, mit dem sich die Gesamtheit aller Kohlenstoffdioxid-Emissionen, die durch die Herstellung, Nutzung oder Entsorgung eines Produktes entstehen. Die Crafting Future GmbH beschäftigt sich mit der Identifikation von Wegen, um die Menge an Emissionen zu verringern.
Aktuell kooperiert das Unternehmen mit dem von der Region geförderten 3D-Druck-Konsortium Hannover, ein Zusammenschluss der 3 Firmen dreiConsulting | Additive Manufacturing Germany GmbH & Co. KG, LikeAbird und Formwerk3D. Diese 3 Firmen betreiben ein Experimentallabor, welches von der Wirtschaftsförderung der Region Hannover unterstützt wird, um kleinen und mittelständigen Unternehmen die Vorteile der Additiven Techniken zu vermitteln.
Das Konsortium unterstützt bei dem Projekt, Bento-Boxen der Crafting Future GmbH zukünftig möglichst ökologisch effizient fertigen lassen.
Bento-Boxen stammen ursprünglich aus Japan. Durch das Ineinanderstapeln von einzelnen Behältern können verschiedene Speisen voneinander getrennt transportiert werden.
Aktuell unterstützt das Projektkonsortium die Crafting Future GmbH bei der Beschleunigung der Produktentwicklung durch iteratives Rapid Prototyping. Dabei werden in kurzer Zeit immer wieder neue Produktversionen gefertigt und getestet. Die jeweils gewonnenen Erfahrungen werden anschließend für weitere Verbesserungen genutzt. In dem Zusammenhang unterstützt das Experimentallabor auch dabei, den Entwicklungsprozess nachhaltiger zu gestalten.
In der aktuellsten Produktvariante werden bereits ausschließlich aus biobasierten und recyclefähige Materialien verwendet, die sich über Schredder und Filamentextruder zu 100 % wieder zu neuen Boxen verarbeiten lassen. Für die Umsetzung wurden vor allem blau-gefärbte Teile aus PLA (polylactic acid) per FDM-Verfahren (Fused Deposition Modeling) hergestellt. Der schwarze Deckel ist aus flexiblem TPU (thermoplastischen Polyurethan) gedruckt - ebenfalls recyclebar.
Sobald das endgültige Design feststeht, plant das Konsortium, auch die Serienfertigung möglichst CO2-neutral auszulegen. Hierfür wird auch das IfBB, das Institut für Biokunststoffe und Bioverbundwerkstoffe der Hochschule Hannover, mit eingebunden.
Kontakt
Dr. Michael Merwart
Region Hannover
Wirtschaftsförderung
Fachbereich Wirtschafts- und Beschäftigungsförderung
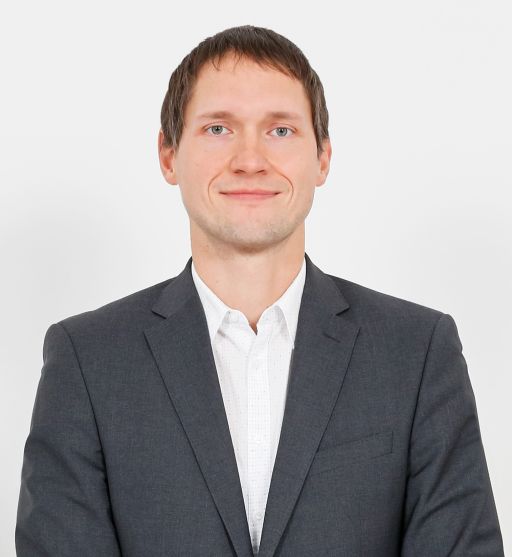